- 0:00 - Dal fine linea al pallettizzatore in modo autonomo
Diva International ha aggiornato le sue linee di produzione con un nuovo impianto di pallettizzazione per le sue salviette umidificate che sfrutta un machine controller e cinque robot mobili autonomi (AMR) di OMRON. Risultato: un processo più sicuro ed efficiente, che tiene traccia di tutti gli step di lavorazione, dall’ordine fino all’evasione in magazzino
Da oltre 30 anni Diva International produce e distribuisce prodotti per la cura e il benessere della persona, l’igiene della casa e la pulizia degli animali da compagnia. Il percorso di espansione dell’azienda umbra è testimoniato dalla crescita del suo stabilimento di produzione, avviato a Spello nel 1999 e ampliatosi anno dopo anno fino ad arrivare agli attuali 20.000 metri quadri.
Fra i più recenti interventi di riqualificazione del sito va annoverato anche il nuovo impianto robotizzato per la pallettizzazione delle salviette, un aggiornamento nato con il preciso scopo di ottimizzare l’efficienza e lo sfruttamento degli spazi all’interno di un sito dalle dimensioni abbastanza ridotte.
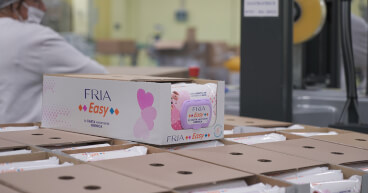
Il progetto di ammodernamento è stato curato dal team di FM Vision che, grazie alla tecnologia e alla consulenza di OMRON, ha fornito una soluzione completamente automatizzata basata sull’impiego di cinque robot mobili autonomi (AMR) in grado di effettuare le operazioni di carico/scarico dei lotti confezionati dal fine linea verso le stazioni robotizzate di pallettizzazione.
Il programma di sviluppo, che è durato complessivamente circa un anno, ha portato anche alla revisione completa dell’architettura di controllo attraverso l’impiego di un machine controller OMRON NJ. Tutto ciò nell’ottica di pervenire a una gestione “olistica” del dato, dall’ordine fino all’evasione dei lotti, e alla creazione di uno storico per il tracciamento di tutte le attività coordinate all’interno dello stabilimento.
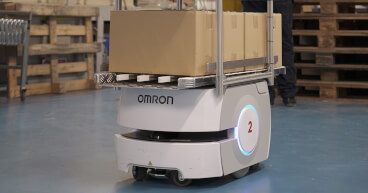
Obiettivo: migliorare la logistica senza modificare gli ambienti
Il nuovo impianto robotizzato di Diva international nasce dall’esigenza primaria di rivedere la logistica di un fine linea ma senza alcun tipo di intervento di ampliamento del locale preesistente, un capannone da circa 240 metri con cinque linee di produzione al suo interno.
Al di là del mantenimento degli spazi, il passaggio da un processo pressoché manuale di smistamento degli imballi sui bancali a uno completamente automatizzato è stato effettuato tenendo conto di tutta una serie di difficoltà oggettive a livello di sicurezza, velocità e pulizia. La sfida più grande è stata quella di progettare un sistema per caricare 12 scatole di cartone nel minor tempo possibile. E farlo gestendo 60 formati diversi da - 40x60 a 400x600 mm - con pesi variabili da 300 grammi a 12 kg. Ad aumentare il coefficiente di difficoltà la necessità di separare l’area di produzione – laddove dove ci sono accumuli di stoffa, polveri e altri materiali contaminanti – da quella di pallettizzazione.
“Un sistema di smistamento e convogliamento su nastro per pacchi con formati così diversi e con queste condizioni al contorno si sarebbe rivelato troppo difficile da realizzare, per evidenti problemi di spazio, ma anche per motivi di costi e sicurezza”, spiega Augusto Falchetti, titolare di FM Vision. “Un flusso di 120 bancali da 70 pacchi l’uno si traduce in circa 8000 pacchi in transito quotidiano: con una perdita di anche solo 1 grammo al giorno, l’accumulo può arrivare a oltre 8 quintali di cartone ogni 100 giorni, con tutto ciò che ne consegue a livello di manutenzione”.
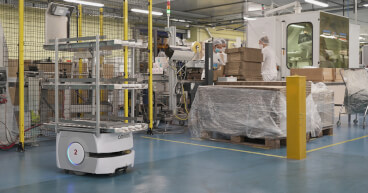