Automatisierungs-Blog

Künstliche Intelligenz in der Industrie 4.0: Zwischen Hype, Hoffnung und FOMO
22. September 2022 Die Angst, etwas zu verpassen, hat in den vergangenen Jahren bedingt durch immer neue Techniktrends, kulturelle Veränderungen, Social Media und Co. beständig an Fahrt aufgenommen. FOMO (Fear Of Missing Out), also die Sorge, Ereignisse, Errungenschaften oder Neuigkeiten zu verpassen, die das eigene Leben verbessern könnten, findet sich dabei in unterschiedlichsten Lebensbereichen, Branchen und Bevölkerungsgruppen. Wenn wir vor zehn Jahren Anfragen zu KI-basierten Projekten erhalten haben, waren diese hauptsächlich von Hype oder FOMO getrieben. Wenn ich damals fragte, warum sich ein Unternehmen mit KI beschäftigen wollte, lautete die Antwort meistens entweder „weil mein Chef mich darum gebeten hat“, „weil wir eine Menge Daten haben“ oder „weil es ein interessantes Feld zu sein scheint“. Keiner dieser Gründe war besonders stichhaltig und rechtfertigte sicherlich nicht die hohen Investitionen, die KI-Anwendungen zu dieser Zeit erfordert hätten.Diese Haltung ändert sich derzeit, und Hoffnung statt Hype oder FOMO wird zur treibenden Kraft. Kunden fragen nicht länger, ob wir ihnen mit KI helfen können. Sie fragen konkret, ob wir ihnen bei vorausschauender Wartung (Predictive Maintenance), Qualitätskontrolle oder Prozessoptimierung unter die Arme greifen können. Sie kommen mit einem Problem zu uns und bitten um Unterstützung für individuelle Herausforderungen. Der Einsatz von KI ist dabei nicht länger ein Motiv oder ein Ziel an sich. Stattdessen ist KI zu einem „Enabler“ geworden – eine Technologie, die Verbesserungen und Vereinfachungen ermöglicht.Egal um welche Branche es dabei geht – Lebensmittel- oder Getränkeindustrie, Pharmazie, Elektronik oder Automobilbau: Die Stoßrichtung ist zumeist dieselbe. Unternehmen wünschen die Herstellung qualitativ hochwertiger, fehlerfreier Produkte zu geringeren Kosten, mit weniger Energieverbrauch und Arbeitsaufwand. KI kann dazu beitragen, diese Ziele zu erreichen.
Flexible Automatisierungs- und Steuerungstechnologien sorgen für nachhaltigere Verpackungen
16. August 2022 Haben Sie schon einmal ein kleines Produkt online bestellt und sich dann geärgert, als es in einem übergroßen Karton mit viel Luftpolsterfolie, Plastik oder Papier bei Ihnen ankam?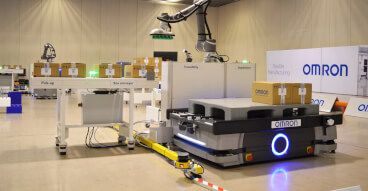
Flexible Manufacturing Roadshow: Das Werk der Zukunft auf Tour quer durch Europa
16. Juni 2022 Wie wäre es, wenn Sie das Werk der Zukunft sehen, fühlen und anfassen könnten? Was ist nötig, um eine flexible, effiziente und nachhaltige Produktion umzusetzen? Das ist die Idee hinter der einzigartigen Flexible Manufacturing Roadshow von OMRON, die in diesem Jahr quer durch Europa unterwegs ist. Auf der Roadshow werden exklusive kollaborative Lösungen für die Zusammenarbeit von Mensch und Maschine vorgestellt.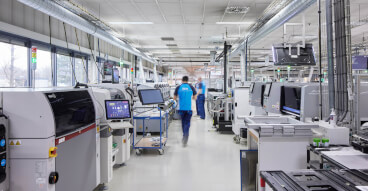
Gemeinsam zum Werk der Zukunft
16. Juni 2022 Als eine der größten Geschäftseinheiten von OMRON wollen wir das Werk 's-Hertogenbosch weiterentwickeln, um den Bedürfnissen in der EMEA-Region gerecht zu werden.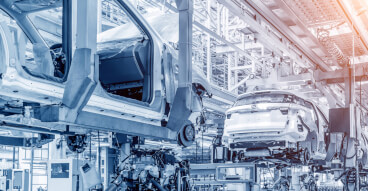
Rückverfolgbarkeit in der Automobilindustrie: Worauf Entscheidungsträger und Experten jetzt achten sollten
23. Mai 2022 Von der E-Mobilität bis zum autonomen Fahren, vom Fachkräftemangel bis zur Digitalisierung: Die Automobilindustrie befindet sich in einem tiefgreifenden Wandel, der unter anderem durch den Wechsel zu globalisierten Plattformen und standardisierten Fahrzeugarchitekturen gekennzeichnet ist. Einerseits wird die Produktion immer effizienter, andererseits kann aber auch schon ein einziges fehlerhaftes Teil weitreichendere Auswirkungen haben als jemals zuvor. Angesichts kostspieliger Rückrufaktionen sehen sich die Automobilhersteller mit immer komplexeren Anforderungen und strengeren Spezifikationen konfrontiert. Lohnt sich der Aufwand für die Rückverfolgbarkeit, wenn dies bedeutet, dass bis zu 20.000 Teile pro Fahrzeug zu kennzeichnen sind? Ja, es lohnt sich, aber es bedarf leistungsfähiger Lese- und Verifizierungstechnologien sowie leistungsstarker Software, um alle Daten sinnvoll nutzen können.Es gibt mehrere Gründe, warum Hersteller genaue Aufzeichnungen über die Teile und Komponenten führen müssen, aus denen ein neues Fahrzeug besteht. Unter Qualitätsgesichtspunkten trägt beispielsweise die Barcodeverfolgung dazu bei, dass die richtigen Teile zusammengebaut werden. Noch wichtiger ist jedoch die Möglichkeit, jedes Fahrzeugteil bis zu seinem ursprünglichen Lieferanten zurückverfolgen zu können. Im Falle eines Rückrufs oder der Entdeckung eines fehlerhaften Teils müssen die Hersteller in der Lage sein, schnell und präzise festzustellen, woher das jeweilige Teil stammt. Hinzu kommen Informationen wie Chargennummer, Herstellungsdatum und andere wichtige Angaben, um zu ermitteln, welche Fahrzeuge von einem fehlerhaften Teil betroffen sind. Empfehlungen und Normen von AIAG, VDA, ANSI und ISO geben hierbei den Rahmen vor. Im Zuge der Globalisierung der Automobilindustrie wird die weltweite Produktion von Leichtfahrzeugen bis 2023 voraussichtlich rund 96 Millionen Einheiten erreichen. Das bedeutet, dass bereits ein einziges fehlerhaftes Teil enorme Auswirkungen haben kann und daher unbedingt zu vermeiden ist.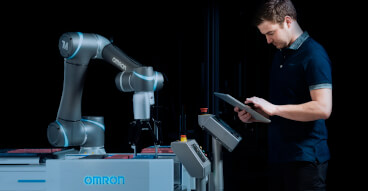
Licht aus in der Fabrikhalle? Mit Industrie 4.0 noch immer unwahrscheinlich
21. April 2022 Für viele Hersteller scheint die Aussicht auf eine vollautomatische, menschenleere Fabrik, Stichwort „Lights out“, noch Lichtjahre entfernt zu sein. Wann, so fragen sie, kommt die 4. industrielle Revolution zu uns, und was können wir erwarten? In diesem Blog diskutieren wir die Wahrscheinlichkeit einer voll-, beziehungsweise halb-automatisierten Fertigung, was Roboter bereits können und was nicht, und warum der Mensch (meistens) immer noch unersetzlich ist.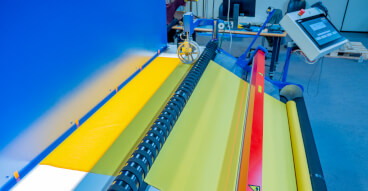
Vadain automatisiert die Inspektion von Vorhang- und Gardinenstoffen mit Bildverarbeitung.
8. April 2022 Vadain, Marktführer im Bereich maßgeschneiderter Vorhänge und Gardinen in den Niederlanden, war auf der Suche nach einer Lösung zur möglichst frühzeitigen Erkennung von Fehlern in kilometerlangen Bahnen von Vorhang- und Gardinenstoffen. Gemeinsam mit den Software-Entwicklern von Sycade, Bildverarbeitungs-Technologie von OMRON und dem Maschinenbauer Eisenkolb wurde eine automatisierte Lösung entwickelt, die Fehler in Vorhang- und Gardinenstoffen erkennt und analysiert. Zeitaufwendige manuelle Inspektionen gehören damit der Vergangenheit an.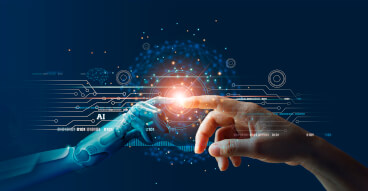
Auch traditionelle Unternehmen sind auf Daten angewiesen
18. März 2022 Die richtigen Tools und Technologien ermöglichen eine fortschrittliche, vorausschauende Wartung, sowie die Vermeidung von Engpässen. Finden Sie heraus, wie die Digitalisierung die Lücke zwischen älteren Systemen und der Industrie 4.0 schließt.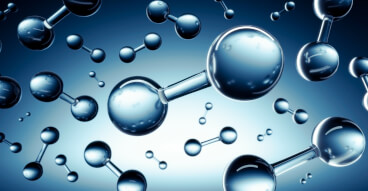
Wasserstoff, Treibstoff für die Zukunft: Hierauf ist bei der Brennstoffzellenfertigung zu achten
10. März 2022 Ist die Rede von nachhaltiger Mobilität, denkt so mancher zuerst an batteriebetriebene E-Autos. Brennstoffzelle oder Wasserstoff-Direktverbrenner sind komplementäre Technologien, die oft in den Hintergrund rücken und doch einiges zu bieten haben, wenn es um CO₂-Reduzierung und Marktoptionen geht.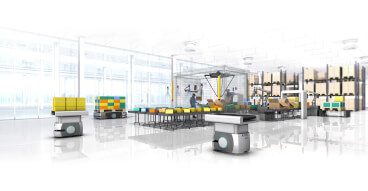
So können E-Commerce-Unternehmen aktuelle Verpackungs- und Intralogistikherausforderungen gelassen meistern
24. Februar 2022 Robotergestützte Verpackungsabläufe ermöglichen eine schnelle und kosteneffiziente Skalierung, um schwankenden Lieferkettenanforderungen gerecht zu werden.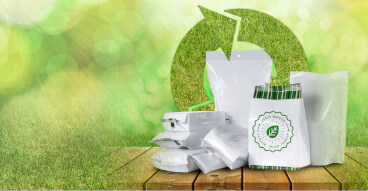
Grüne Verpackungsindustrie: Hierauf sollten Unternehmen in Sachen Nachhaltigkeit vermehrt achten
9. Februar 2022 Nachhaltigkeit in der Verpackungsindustrie ist eine der zentralen Herausforderungen im Kampf gegen das weltweite Plastikmüllproblem und den Klimawandel. Flexible und leistungsstarke Automatisierungstechnologie ist gefragt.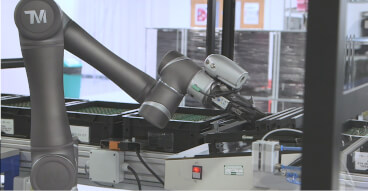
Hanover Displays automatisiert PCBA-Tests mit Cobots
31. Januar 2022 Das in Großbritannien ansässige Unternehmen Hanover Displays Limited war auf der Suche nach einem neuen System zum Testen von Platinenbaugruppen (PCBAs, Printed Circuit Board Assemblies) und entschied sich für TM Cobots von OMRON. Geliefert und installiert wurde alles von Absolute Robotics, einem Unternehmen der Absolute Automation Group.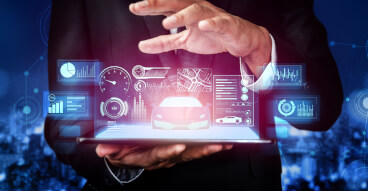
Der Konkurrenz die Stirn bieten: So gewinnen europäische Automobilunternehmen an Wettbewerbsstärke
29. Januar 2021 In der Automobilindustrie läuft die Konkurrenz aus Asien Europa vermehrt den Rang ab. Deshalb suchen Automotive-Player nach innovativen Wegen, die sie effizienter, nachhaltiger und zukunftssicherer machen. Der Wirtschaftswissenschaftler Tony Seba geht davon aus, dass im Jahr 2025 keine Neufahrzeuge mit (reinem) Verbrennungsmotor mehr verkauft werden. Doch ob sich batterie- oder wasserstoffbetriebene Brennstoffzellen durchsetzen werden, ist derzeit noch unklar – es werden wohl verschiedene Antriebsarten sein. Umsatzrückgänge, Abgasvorschriften, neue Technologien, Digitalisierung und veränderte Verbraucherbedarfe sind weitere Entwicklungen auf diesem Gebiet. Ihnen lässt sich nur begegnen, wenn Unternehmen jetzt ihre Fertigungslinien umstellen, flexibler und innovativer agieren, um sich so Wettbewerbsvorteile zurückzuerobern.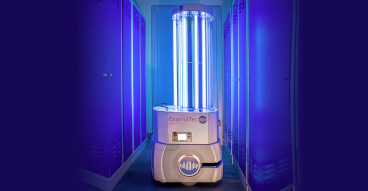
ControlTec unterstützt polnisches Krankenhaus mit einem mobilen UVC-Roboter bei der Pandemiebekämpfung
26. Januar 2021 Gesundheitseinrichtungen auf der ganzen Welt suchen nach automatisierten Lösungen für die sichere Desinfektion einzelner Räume und öffentlicher Bereiche, um einer Reihe neuer Hygieneverfahren im Rahmen der Covid-19-Pandemie gerecht zu werden. Der polnische Systemintegrator ControlTec hat hierzu einen mobilen Roboter, auf Grundlage des Roboters OMRON LD, entwickelt. Damit ist ControlTec eines der ersten Unternehmen weltweit, das einen Sterilisationsroboter, der mit einem UVC-Strahler ausgestattet ist, auf den Markt gebracht hat.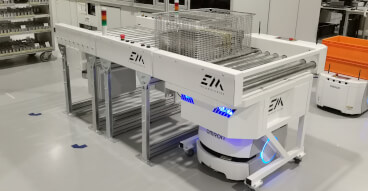
Flott und sicher durch die Fabrikhalle
18. Januar 2021 Verbesserte OEE und nahtlosere Materialversorgung: Philips Austria GmbH Klagenfurt automatisiert Materialtransport mit autonomen mobilen Robotern (AMR) von OMRON.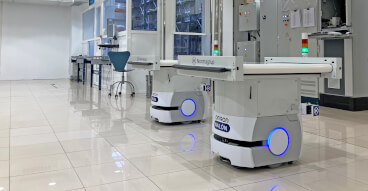
Verbesserte Flexibilität, Agilität und Rückverfolgbarkeit mit mobilen Robotern für Normagrup
6. Januar 2021 Normagrup, ein auf technologisch fortschrittliche Beleuchtung spezialisiertes Unternehmen, musste den Materialtransport zwischen drei Produktionsbereichen, dem Montagebereich und einem automatisierten Lager automatisieren. Das umfasste auch die Navigation durch enge Räume, in denen sich Werkspersonal aufhält.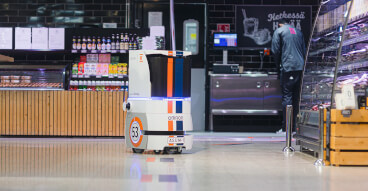
Mobiler Roboter optimiert die Lebensmittellieferung
30. November 2020 Vor Kurzem konnte ein pfeifender autonomer mobiler Roboter in den Fluren eines Einkaufszentrums in Helsinki, Finnland, gesichtet werden. Der vom OMRON-Vertragspartner Dimalog betriebene Roboter nahm an einem einmonatigen Versuch des automatisierten Zustellservice „Home on Demand“ teil.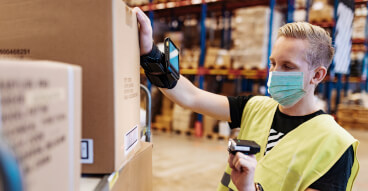
3 Auswirkungen von COVID-19 auf die Logistikabläufe in Großbritannien (und welche Maßnahmen man ergreifen kann)
4. November 2020 Von Stuart Coulton, Regional Manager, OMRON UK North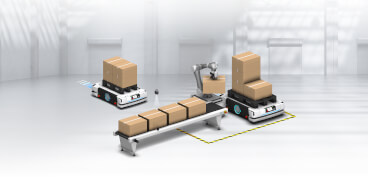
Top Tipps für die Auswahl mobiler Roboter für schwere Lasten
11. September 2020 Fünf Fragen, die sich Industrieunternehmen in Sachen autonome Materialtransporttechnologie stellen sollten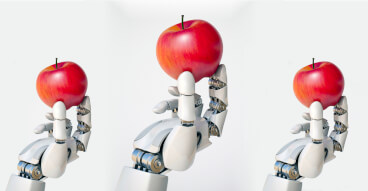
Fabrikautomatisierung: Vier Tipps für die Zukunft der Lebensmittel- und Getränkeherstellung
16. Juli 2020 Die Coronavirus-Pandemie hat Unternehmen jeder Art und Größe vor große Herausforderungen gestellt. In der Lebensmittel- und Rohstoffindustrie sehen sich Unternehmen eines deutlichen Rückgangs des Verbrauchs und einer Unterbrechung der Lieferketten gegenübergestellt, während der Verbrauch zu Hause zugenommen hat und der Verbrauch außer Haus fast zum Stillstand kam. Aber wie können Hersteller ihre Geschäftsstrategien und Produktionsprozesse aktuell und langfristig anpassen? Die Pandemie kann eine Chance sein, veraltete Prozesse und Verfahren zu überdenken und sie mit Konzepten wie innovativer Robotik, Sensortechnologie und ganzheitlichen Automatisierungsstrategien zu erweitern.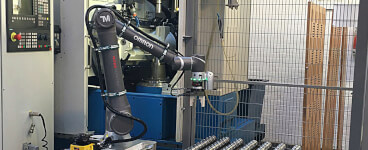
Cobots verschaffen Getriebehersteller einen Wettbewerbsvorteil
14. Mai 2020 Der dänische Getriebehersteller Fischer Gears hat die Wettbewerbsfähigkeit seines Produktionsprozesses – besonders bei größeren Serien – durch die Installation von zwei Omron TM-Robotern gesteigert. Die kollaborativen Roboter (Cobots) ermöglichen es erfahrenen Mitarbeitern, sich auf wertschöpfendere Aufgaben zu konzentrieren.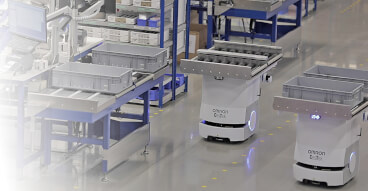
Auftragsfertigung mit einer fortschrittlichen Flotte mobiler Roboter
11. Mai 2020 VOLA, ein dänischer Hersteller von Sanitär- und Küchenarmaturen der Luxusklasse, hat ein neues Werk eröffnet, in das neun mobile Roboter von Omron integriert sind.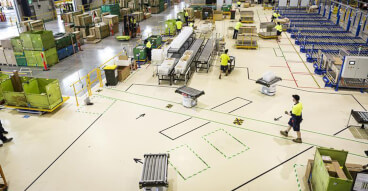
Mobile robots smarten up Toyota’s new parts centre
28. April 2020 Intelligent robots and sophisticated design are helping Toyota to achieve a higher level of efficiency at its new warehouse in Sydney, Australia.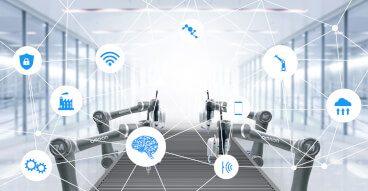