Diese vier Herausforderungen müssen E-Auto-Hersteller auf dem Weg zu mehr Nachhaltigkeit meistern
Veröffentlicht am 17. Juni 2024 in Sustainable Manufacturing
Zunächst als Utopie abgetan, dann mit großen Augen bestaunt und nun in immer mehr Garagen zu finden: Elektrofahrzeuge haben sich innerhalb weniger Jahre von einem Nischenmarkt zu einem mächtigen Wirtschaftsfaktor entwickelt. Der Anteil der E-Autos (BEV) an allen Pkw-Neuzulassungen lag im Juni 2024 beispielsweise bei 14,6 Prozent. Im gesamten Jahr 2024 sollen laut IEA 17 Millionen E-Fahrzeuge weltweit verkauft werden – das entspricht einer Steigerung von 20 Prozent gegenüber 2023. Experten gehen davon aus, dass sich dieses Wachstum weiter fortsetzen wird. Dass Regierungen weltweit darauf drängen, CO2-Emissionen weiter zu reduzieren, wird die Umstellung auf Elektrofahrzeuge zudem weiter beschleunigen.
Doch was bedeutet das für die Hersteller von E-Autos? Zum einen müssen sie sich auf die Entwicklung und Produktion vorwiegend elektrischer Flotten umstellen – ein Schritt, den die meisten Automotive-Player bereits vollzogen haben. Zweitens müssen sie neue Produktionslinien aufbauen und Fertigungsabläufe rationalisieren, was häufig eine große Herausforderung darstellt. Ein erfahrener Automatisierungspartner kann hierbei wertvolle Schützenhilfe leisten, etwa wenn es darum geht, eine komplexe Umstellung zu bewerkstelligen. Mit seinem innovativen Technologieportfolio, einem globalen Support-Netzwerk und fundierter Expertise in der Automobilindustrie kann OMRON Hersteller auf ihrem Weg zur Elektrifizierung flexibel und umfassend begleiten. In diesem Beitrag haben wir die größten Herausforderungen in der EV-Fertigung für Sie zusammengefasst. Zugleich erfahren Sie, wie Hersteller ihre Produktion zukunftsstark aufstellen können.
Herausforderung 1: Überladung, Überentladung und Überstrom in Batterien
Lösung: Die Herstellung von Batterien und Brennstoffzellen erfordert eine präzise Kontrolle der Elektrodendicke, um Überladung, Überentladung und Überstrom zu verhindern. OMRON ermöglicht doppelseitige Dickenüberprüfung, bei der sowohl von der Ober- als auch von der Unterseite des Blechs gemessen wird, was genauere Messungen als bei herkömmlichen einseitigen Methoden ermöglicht. Zudem setzt OMRON auf RFID- und 2D-Codes zum Managen von Zeit und Zellkapazität, um sicherzustellen, dass Batteriepacks aus Zellen mit identischen Kapazitäten hergestellt werden und gleichbleibende Leistung aufweisen.
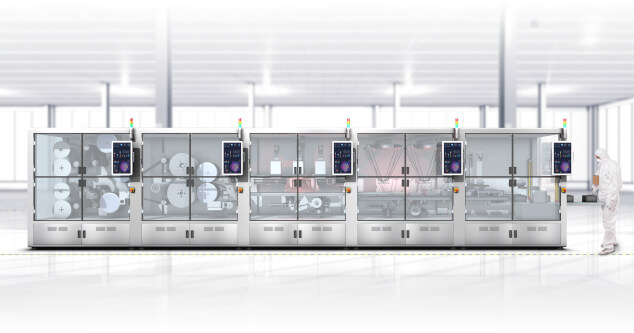
Herausforderung 2: Zunahme elektrischer Steuereinheiten (ECUs)
Lösung: Mit der vermehrten Elektrifizierung von Fahrzeugen steigen auch die Anzahl und Komplexität der Steuergeräte. Herkömmliche Methoden zur Konfiguration von Prüfeinstellungen für jeden Steckerstift sind extrem zeitaufwändig und auch teuer. OMRONs Lösung für die Steckerprüfung vereinfacht diesen Prozess, da hierbei ein weniger komplexes Algorithmusdesign benötigt wird. So können Hersteller ihre Produkte nahtlos in die Fertigung integrieren und verbundene Kosten effektiv verwalten, während sie gleichzeitig die Anforderungen einer sich schnell entwickelnden Branche erfüllen.
Herausforderung 3: Effiziente und verlässliche Schweißnahtprüfungen
Lösung: Schnelle und genaue Schweißnahtprüfungen sind essentiell, vor allem bei Hochleistungsmotoren mit vielen Schweißpunkten. Die fortschrittliche Bildverarbeitungstechnologie von OMRON ermöglicht stabile und schnelle Kontrollen. Zugleich lassen sich Qualitätsprüfungen schneller durchführen. Diese Technologie nutzt einen einzigartigen Kontrollalgorithmus für High-Speed-Inspektionen. Prüfzeiten lassen sich so deutlich verkürzen und verlässliche Genauigkeit sicherstellen.
Herausforderung 4: Arbeitssicherheit in der Endmontage
Lösung: In Fertigung und Endmontage nimmt auch die Sicherheit der Mitarbeiter eine immer wichtigere Rolle ein. Die autonomen mobilen Roboter (AMR) von OMRON, wie die Technologien der LD-Serie oder der HD-1500 für schwere Lasten, wurden entwickelt, um Gabelstapler zu ersetzen und so Sicherheit und Effizienz zu verbessern. Diese Roboter transportieren schwere Nutzlasten ohne Probleme und navigieren dabei sicher und autonom durch Industrieumgebungen. Sie helfen, das Verletzungsrisiko zu verringern und dem Fachkräftemangel proaktiv und wirksam zu begegnen.
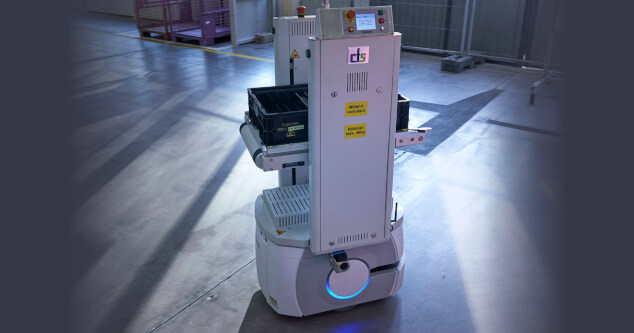