So gelingt der erfolgreiche Start in digitale Fertigungsabläufe
Veröffentlicht am 12. November 2024 in Industry 4.0
Warum es sich lohnt, Produktionsabläufe zu digitalisieren
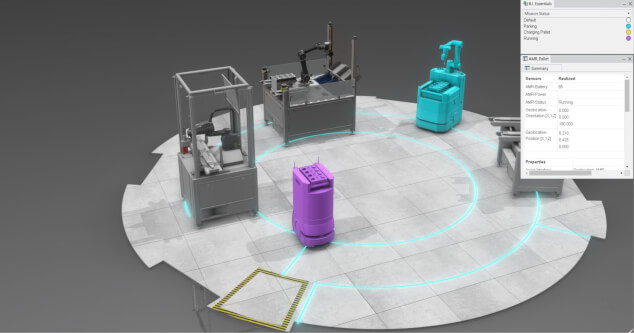
Virtuelle Modelle neuer Maschinen oder Anlagen helfen Unternehmen, Projektrisiken zu verringern und die Zeit, die für den Aufbau und die Prüfung von Anlagen benötigt wird, drastisch zu reduzieren, denn kostspielige Fehler können in der virtuellen statt in der realen Welt gemacht werden. Das ist für jeden Player der Fertigungsindustrie von Vorteil, vor allem aber für die Automobilindustrie, da sie einem enormen Druck unterliegt, die Markteinführung neuer Produkte zu beschleunigen und das Fehlerrisiko zu minimieren.
Die Vorteile der Digitalisierung enden nicht mit der virtuellen Inbetriebnahme. Sie ist erst der Anfang. Der virtuelle Zwilling spiegelt das physische System in Echtzeit wider und lässt sich während der gesamten Lebensdauer eines Systems oder Produkts nutzen, so dass immer wieder in einer sicheren parallelen digitalen Umgebung geprüft werden kann, wie sich neue Materialien, neue Bestandteile oder neue Werkzeuge verhalten werden.
Außerdem lässt sich die kontinuierliche Überwachung der Maschine oder des Prozesses für vorbeugende Wartung, Zustandsüberwachung, Energiemanagement und OEE (Gesamtanlageneffektivität) nutzen.
Digitalisierte Fertigung ist zudem Voraussetzung für Losgröße eins, also das Konzept, jedes Produkt in jeder Variante in jeder Menge und in jeder Reihenfolge herstellen zu können. Dieser Ansatz entwickelt sich vor allem in der pharmazeutischen Industrie zunehmend zu einem Unterscheidungsmerkmal: Neue Arzneimittel für seltene Krankheiten und modernste Diagnostik ermöglichen es, Patienten mit dem besten Arzneimittel in der für sie optimalen Dosis zu behandeln.
Mittels durchdachter Digitalisierung können Firmen Risiken mindern, Produktionsabläufe beschleunigen und Geschäftsmodelle mit einer noch nie dagewesenen Flexibilität ausstatten.
Wie lassen sich Fertigungsabläufe bestmöglich digitalisieren?
Der Schlüssel zur erfolgreichen Realisierung einer digitalen Produktionsstätte liegt in der Verbindung von IT und OT. Jahrelang galt dieses Zusammenspiel als unmöglich, weil sie so unterschiedlich sind – als ob Marsmenschen und Venusbewohner miteinander sprechen sollen.
In der digitalen Fertigung muss alles, von der Sensorik bis zum Bestellsystem, Teil eines standortweiten Netzwerks sein. Aber es reicht nicht, dass alle Funktionen miteinander verbunden sind – sie müssen auch in der Lage sein, Daten zu generieren und diese auszutauschen. Außerdem müssen sie wissen, wie sie die gesammelten Informationen interpretieren und umsetzen können. Wird dem Bestellsystem etwa mitgeteilt, dass ein Kunststoff nicht verfügbar ist und stattdessen ein Ersatzmaterial mit einer leicht abweichenden technischen Spezifikation geliefert wird, muss die Bestellfunktion dies an die Fertigungslinie weitergeben, damit die Maschineneinstellungen entsprechend angepasst werden können. Cyberphysische Systeme sind die Bausteine dieser Netze und stellen die Verbindung zwischen den verschiedenen Komponenten her.
Selbstlernende und adaptive Systeme stellen eine weitere Säule erfolgreicher Digitalisierung dar. Algorithmen des maschinellen Lernens werden eingesetzt, um große Mengen von Produkt-, Linien- und Maschinendaten zu verarbeiten. Hierdurch können Hersteller zeitaufwändige Aspekte des Fertigungsprozesses optimieren, darunter Qualitätskontrolle, Anlagenwartung und Produktdesign.
Ebenso wichtig ist es, Menschen und Maschinen dazu zu bringen, harmonisch miteinander zu arbeiten. Durch den Einsatz von KI und Robotik können Hersteller von der Interaktion zwischen Mensch und Maschine profitieren. So lässt sich die Fertigung zu einem neuen Paradigma der Flexibilität und Individualisierung führen.
All dies erfordert zweifelsohne eine enge und langfristige Kooperation mit starken Partnern. Die Fertigungsindustrie kann das große Potenzial der Digitalisierung nur dann nutzen, wenn Experten aus verschiedenen Fachbereichen zusammenarbeiten. Dies können Partnerschaften mit Kunden, Lieferanten, Dienstleistern, Unternehmen anderer Branchen, akademischen Instituten, Start-ups und sogar Wettbewerbern sein. Teamarbeit führt zu komplexen Geschäftsökosystemen und Synergien, die zu bahnbrechenden Lösungen führen kann.
Der genannte Partnerschaftsansatz erfordert Offenheit – die meisten Maschinenbauer weigern sich jedoch, die internen Funktionen ihrer Maschinen offenzulegen, weil sie fürchten, so ihr Geschäftsgeheimnis zu verraten. Die einzige Möglichkeit, die beiden Welten von OT und IT zusammenzubringen, besteht aber darin, Ökosysteme zu schaffen, die auf gegenseitigem Vertrauen beruhen.
OMRONs Partner im Bereich der digitalen Fertigungsplanung ist Dassault Systèmes. Die Kombination der Fähigkeiten beider Unternehmen im ISA-95-Funktionsmodell, das häufig als Rahmen für die digitale Fertigungsplanung dient, bildet eine ideale Ergänzung, ein vollständiges ISA-Modell mit den Kompetenzen beider Player.
Digitalisierung spielt unbestreitbar eine wichtige Rolle auf dem Weg zu immer größerer Flexibilität und Anpassbarkeit, kürzeren Innovationszyklen und nachhaltigerer Produktion in diversen Fertigungsindustrien. In nicht allzu ferner Zukunft wird voraussichtlich alles – von E-Fahrzeugen über Antibiotika bis zu Schokolade und Lippenstiften – in digitalen Fertigungsstätten hergestellt werden.
Kontaktieren Sie uns, um weitere Informationen zu erhalten